Istoria industriei siderurgice
Pentru a înțelege istoria industriei siderurgice , este necesar să aveți în vedere următoarele definiții:
- Fier : în prezent, acest termen se referă la elementul chimic Fe sau fier pur (care se topește la aproximativ 1538 ° C, [1] are proprietăți tehnologice foarte slabe și este foarte ușor de oxidat); dar în antichitate și până în secolul al XIX-lea , cuvântul a identificat acel tip special de fier care era maleabil la căldură și nu a luat întărirea . Astăzi, același metal se numește fier moale sau, mai bine, oțel foarte scăzut de carbon.
- Fier forjat : fier maleabil, deasupra.
- Oțel : aliaj fier-carbon, cu un conținut în greutate de carbon [2] de până la 2,11%. În cele mai vechi timpuri și până în secolul al XVIII-lea, se credea că este un anumit tip de fier căruia îi lipsea ceva. A fost obținut în cuptoare închise sau prin adăugarea parțială de fontă la fier în creuzete: caracteristica sa a fost „fragilitatea”, adică rezistența sa scăzută la fracturi la rece și durabilitatea la căldură.
- Fontă : aliaj fier-carbon, cu un conținut în greutate de carbon mai mare de 2,11%. Este prea fragil pentru a fi procesat pentru a fi fabricat . Fonta a fost obținută din cuptoare închise de o anumită fabricare, suflate cu mașini mișcate de roți hidraulice începând cu secolul al XII-lea în Suedia, Germania și nordul Italiei. Din fontă sau oțel s-a obținut în forje, care au fost alimentate și cu burduf hidraulic. [3]
Informații istorice
Chiar dacă astăzi încă nu știm care dintre popoarele antice a produs în mod conștient fierul și oțelul, este acum sigur că în orice caz prima utilizare a acestor materiale este mult mai devreme decât începutul acelei ere la care ne referim ca Fierul Vârsta .
Primul fier folosit a fost cel prezent în meteoriți deja în epoca preistorică , dovadă fiind conținutul ridicat de nichel al descoperirilor arheologice din epoca cea mai veche.
Odată ce ați învățat cum să lucrați la forjă , pasul pentru a ajunge la topirea minereurilor de fier nu a fost foarte lung, deoarece procesul de reducere a minereurilor de cupru ( epoca bronzului ) era acum cunoscut.
Conform stării actuale de cunoaștere, fierul a apărut pentru prima dată în Asia Mică, iar primele dovezi sunt atribuite calibilor , care au trăit la sud-est de Marea Neagră .
Aliaje de fier - fier maleabil, fontă și oțel - au început să apară și în secolul al XII-lea î.Hr. în India , Anatolia și Caucaz .
Utilizarea fierului, în aliaje și în forjarea uneltelor, a apărut în Africa subsahariană în anii 1200 î.Hr. [4] .
Mărturii importante ale fierului în antichitate sunt comoara de fier a regelui babilonian Sargon II din Ninive , performanțele remarcabile ale egiptenilor în domeniul siderurgiei și tehnologia extrem de dezvoltată a construcției armelor de către romani și norieni . În pământul germanic, începuturile producției de fier se pierd în legendă.
Edda , Weland Saga și Cântecul Nibelungilor demonstrează marea stimă în care era ținut fierarul și, în special, fierarul.
Prezența fierului în pământul germanic este dovedită istoric până la începutul primului mileniu î.Hr , dovadă fiind numeroasele descoperiri arheologice datând din acea vreme, cum ar fi hașe și vârfuri de lance.
Dezvoltarea treptată a artei siderurgice a avut loc în principal în locuri în care au fost descoperite minereuri de fier ușor reductibile și a fost disponibil lemn suficient pentru a obține cărbunele necesar procesului siderurgic.
Minereurile de fier, mai ales după spălare și prăjire, au fost topite cu cărbune în groapă sau cuptoare de groapă din lut, piatră de carieră sau tăietori de pietre .
Cuptoarele utilizate în acest scop, pe care astăzi le-am numi „reducere directă” sau catalană , funcționau inițial cu tiraj natural.
Mai târziu, proiectul a fost asigurat de burdufuri manuale.
Produsul finit consta dintr-o masă mare de fier forjat sau oțel amestecat cu zgură (flori) care, cu încălzire și forjare repetate, a fost eliberată de aderență și a inclus zgură și, de obicei, imediat transformată în produse finite.
Când la sfârșitul secolului al XIV-lea tehnica din China a ajuns în Europa prin arabii burdufului acționați de energie hidraulică, ambii au ridicat treptat pereții cuptoarelor ajungând în cuptoarele cuvei.
Acest lucru a furnizat, la fel ca cuptorul cu reducere directă, un produs care, odată eliberat de zgură, a fost direct uitat, dar a fost mult mai mare și a fost numit lingou.
Drept urmare, forța musculară a fierarului nu mai era suficientă pentru a forja lingoul și a recurs din nou la energia hidraulică pentru a acționa ciocanele de forjare.
Transformarea tehnologică profundă care a condus la afirmarea furnalului trebuie să fie atribuită exploatării termice mai bune a cuptorului cuva în care, datorită creșterii temperaturii realizate, fierul a ajuns să atingă temperatura de topire și să toarne în stare lichidă. a fi obținute în mase plastice.
Nu există informații fiabile despre începuturile utilizării furnalelor și nici nu se știe unde a fost obținută prima fontă, totuși este sigur că utilizarea fontei era deja cunoscută în mileniul I î.Hr.
Cu siguranță utilizarea cuptorului nu se datorează unei descoperiri întâmplătoare, deoarece tehnica de producție a metalului topit era bine cunoscută pentru producția de plumb, staniu și cupru.
Comparativ cu oțelul obținut, cu procesul direct, imediat din minereu de fier, fonta avea un conținut ridicat de carbon și nu era forjată.
Pentru a-l transforma în oțel, a trebuit mai întâi să fie rafinat .
În funcționarea vechilor fondatori, acest proces a fost o purificare.
La rafinare, elementele străine conținute în fontă (exces de carbon, siliciu, mangan etc.) au fost „arse” de un foc de cărbune cu exces de aer, adică cu o atmosferă conținând dioxid de carbon și oxigen .
Primele urme ale producției industriale de fontă cu furnale datează de la începutul secolului al XIV-lea.
Numai în jurul anului 1400 a apărut fonta aproape simultan în Italia și Germania și una dintre primele sale aplicații a fost turnarea de ghiulele.
Cu toate acestea, nu este încă clar ce rol au jucat experiențele țărilor occidentale în dezvoltarea furnalului și ce parte, cu siguranță, o cunoaștere mult mai veche a topitorilor din Asia de Est.
Fonta a fost inițial obținută prin topirea bucăților de fontă sau resturi de fier în cuptoare de reverberare sau cuptoare cu groapă mică sau prin preluarea fontei direct din furnale (prima fontă turnată).
În 1500 turnarea în fontă a ajuns la o utilizare generalizată, începând de la Siegerland unde s-a dezvoltat ca o ramură importantă a industriei siderurgice cu turnarea țevilor, clopotelor, grilelor etc.
O transformare radicală a industriei siderurgice a avut loc atunci când, din cauza epuizării progresive a disponibilității lemnului, a fost forțată să folosească cărbune tare și cocs pentru a înlocui cărbunele din furnalele.
Abraham Darby II din Coalbrookdale a fost primul care a reușit în 1709 să obțină fontă folosind doar cocs.
Cu toate acestea, nu s-a știut cum să se transforme fonta, produsă în cantități mari, în oțel cu aceeași viteză de producție, având în vedere că capacitatea de producție a cuptoarelor de rafinare era foarte limitată.
A mai durat câteva decenii să învețe cum să înlocuiască cărbunele tare pentru lemn chiar și în producția de oțel.
Dificultățile constau în special în necesitatea ca oțelul să nu intre în contact cu cărbunele sau cocsul pentru a nu absorbi sulful și, prin urmare, să devină fragil atunci când este fierbinte.
Acest inconvenient a fost eliminat de Henry Cort în cuptorul său de băltoace inventat în 1784, în care oțelul a intrat în contact doar cu produse de ardere foarte bogate în oxigen. Pentru a expune continuu baia la gazele reducătoare a fost agitată; din această operațiune procedura a avut denumirea de "puddellatura" (de la to puddle : to mix).
Odată ce utilizarea cărbunelui dur a fost introdusă atât în producția de fontă, cât și în cea a oțelului, furnizarea de combustibili nu a mai constituit o dificultate pentru dezvoltarea industriei siderurgice.
Dezvoltarea industriei siderurgice a găsit, la sfârșitul secolului al XVIII-lea și începutul secolului al XIX-lea, un nou ajutor puternic în motorul cu aburi.
Acest lucru a fost folosit nu numai pentru a îmbunătăți pescajul, ci a permis construirea de mașini de transformat, cum ar fi laminare și ciocane, în dimensiuni mult mai mari și, prin urmare, cu performanțe mai bune.
De la momentul primului furnal, au fost aduse diverse îmbunătățiri la acesta, ambele având ca scop creșterea capacității de producție și simplificarea funcționării.
Printre acestea se numără duza de zgură Luhrmann, o conductă de încărcare a zgurii răcită cu apă, care din 1867 a fost instalată sub duzele de aer în locul frunții folosite până atunci.
Acest dispozitiv a făcut posibilă creșterea semnificativă a presiunii aerului și, odată cu aceasta, a capacității de producție a cuptorului și a pus capăt întreruperilor frecvente în funcționare.
Și mai remarcabile au fost transformările din industria siderurgică din secolul al XIX-lea.
În secolele al XVIII-lea și al XVIII-lea, calitățile oțelului cu o duritate mai mare au fost obținute prin cimentare , un proces constând în încălzirea tijelor sau șinelor în oțel moale în prezența materialelor care conțin carbon (de exemplu cărbune).
Cu acest proces, carbonul a pătruns în oțel, sporindu-i duritatea.
Cu toate acestea, deoarece conținutul de carbon a fost distribuit inegal în fiecare bară, s-a încercat o distribuire mai bună a carbonului pe întreaga bară, supunându-l forjării la cald; produsul astfel obținut a fost denumit „oțel omogen”.
Pentru a obține o omogenitate mai mare, Benjamin Huntsman a fost primul care a întreprins în 1740 topirea pieselor de oțel cimentat într-un creuzet , devenind primul care a obținut oțel topit. Pe termen lung, însă, cererea de oțel nu mai putea fi satisfăcută doar cu procesul de bălțare.
În 1885, englezul Henry Bessemer a reușit să producă oțel cu un proces mai simplu [5] . Procedura sa a constat în suflarea unor curenți puternici de aer prin fonta topită, rezultând arderea substanțelor care însoțeau oțelul, precum carbonul, siliciul, manganul etc. Cu toate acestea, procesul Bessemer a fost limitat la câteva fierărie, deoarece numai fontele fără fosfor ar putea fi tratate cu aceasta, datorită acoperirii interne a convertorului , un vas în formă de pară în care a avut loc operația. De fapt, Bessemer a folosit un strat bogat în acid silicic care nu a putut forma zgură care se leagă de fosfor.
Această problemă s-a confruntat cu Sidney Gilchrist Thomas, care în 1879 a acoperit convertorul cu var amestecat cu silicați solubili.
Zgura obținută prin procedeul Thomas , având un anumit conținut de fosfați, era potrivită pentru utilizare ca îngrășământ .
Majoritatea oțelului produs astăzi, în plus față de procesul Bessemer, este produs cu procesul Martin-Siemens , numit după inventatorii săi Pierre și Emile Martin și Carl Wilhelm Siemens . Inițial, în 1864, procesul consta în topirea fontei împreună cu resturile de fier (procesul de fier-resturi); mai târziu, fonta a fost topită cu minereuri de fier, frecvent cu adăugarea de resturi de oțel (fontă-proces mineral). Topirea trebuia să aibă loc într-un cuptor special conceput, cu focar de recuperare a căldurii, proiectat de Friedrich Siemens .
În prima jumătate a secolului al XIX-lea, oțelul era încă destul de scump: 50-60 GBP pe tonă, comparativ cu 3-4 GBP pentru fontă.
Fier meteoritic

Fabricarea obiectelor de uz comun începând cu fierul meteoric este urmărită în secolul al III-lea î.Hr. [6]
Datorită faptului că meteoritii cad din cer, unii lingviști au speculat că cuvântul englez iron (engleza veche: i-sern ), care are rude în multe limbi nordice și occidentale, derivă din aisar etrusc , care înseamnă „Zeii ". [7] Chiar dacă nu ar fi fost cazul, cuvântul a fost probabil importat în limbile pre -proto-germanice , din cele celtice sau italice . [8] [9] Krahe compară formele în irlandezul vechi, iliric , venețian și messapian . [10] Originea meteoritică a fierului în prima sa utilizare de către bărbați [11] este menționată și în Coran :
„Într-adevăr, am trimis mesagerii noștri cu dovezi fără echivoc și am trimis Scriptura și Balanța cu ei, astfel încât oamenii să respecte dreptatea. Am dus jos fierul, un instrument teribil și util pentru oameni, astfel încât Allah să recunoască cine îl sprijină pe El și pe solii Săi în ceea ce este invizibil. Allah este puternic, înălțat " |
( Coranul 57:25 ) |
Fierul avea o utilizare limitată înainte de a fi posibil să se topească. Primele semne ale utilizării fierului provin din Egiptul antic și sumerieni , unde în jurul anului 4000 î.Hr. erau produse mici obiecte de fier meteorit ca ornamente sau ca puncte de suliță . [12] Cu toate acestea, utilizarea lor pare a fi ceremonială, iar fierul era un metal scump: de fapt în 1600 î.Hr fierul costa de cinci ori mai mult decât aurul și de patru ori mai mult decât argintul . Unii meteoriți (numiți „sideriți” sau „meteoriți feroși”) conțin un aliaj de fier și nichel [13], iar fierul recuperat din căderile de meteoriți le-a permis vechilor să fabrice câteva mici artefacte de fier.
În Anatolia , fierul topit era uneori folosit pentru armele ornamentale: un pumnal cu o lamă de fier și o manetă de bronz a fost găsit dintr-un mormânt hitit datat din 2500 î.Hr. Împăratul egiptean Tutankhamun care a murit în 1323 î.Hr. a fost de asemenea îngropat împreună cu un pumnal de fier cu o mana aurie. O sabie egipteană antică purtând numele faraonului Merneptah și un topor de luptă cu o lamă de fier și un mâner de bronz decorat cu aur au fost de asemenea găsite în săpăturile din Ugarit . [14] Hitiții timpurii au negociat cu asirienii o greutate de fier pentru 40 de argint . Fierul cu meteorit a fost folosit pentru a împodobi instrumentele din America de Nord precolumbiană. Începând cu anul 1000, poporul groenlandez din Thule a început să fabrice harpoane și alte instrumente ascuțite din bucăți de meteorit din Cape York . [15] [16] Aceste artefacte au fost folosite și ca marfă cu alte populații arctice: instrumente fabricate din meteoritul Cape York au fost găsite în situri arheologice aflate la mai mult de 1.600 km distanță. Când exploratorul american Robert Edwin Peary a adus cel mai mare fragment al meteoritului la muzeul american de istorie naturală din New York în 1897 , acesta cântărea încă peste 33 de tone . [17]
Orientul Mijlociu
Preistorie și antichitate

Primele dovezi ale utilizării fierului provin de la sumerieni și egipteni , care l-au folosit deja cu 4.000 de ani înainte de Hristos pentru fabricarea unor obiecte mici, precum vârfuri de suliță și bijuterii, realizate din fier recuperat din meteoriți .
Multe obiecte din fier forjat datează din perioada 3000 î.Hr. până în 2000 î.Hr. (se disting de obiectele fierului meteoric din cauza lipsei de nichel din aliaj ), găsite în Mesopotamia , Anatolia și Egipt ; utilizarea lor pare a fi ceremonială : fierul era de fapt un metal scump, chiar mai mult decât aurul . În Iliada majoritatea armelor și armurilor menționate sunt fabricate din bronz , [18] [19] [20], iar bulgări de fier sunt folosiți pentru comerț. În jurul anului 1500 î.Hr, apar din ce în ce mai multe obiecte de fier în Mesopotamia , Anatolia și Egipt . [21]
Ipoteza creșterii fierului asupra bronzului
Între secolul al XII-lea î.Hr. și secolul al X-lea î.Hr. , fierul a înlocuit bronzul în producția de instrumente și arme în estul Mediteranei ( Levant , Cipru , Grecia , Creta , Anatolia și Egipt ). [22] [23] Deși obiectele de fier au fost cunoscute din epoca bronzului de -a lungul estului Mediteranei, ele se găsesc doar sporadic și sunt statistic nesemnificative în comparație cu cantitatea de obiecte din bronz din aceeași perioadă. [24] Această tranziție, care a avut loc în momente diferite în diferite regiuni ale planetei, marchează începutul etapei civilizației cunoscută sub numele de „ Epoca fierului ”. O explicație acum discreditată a creșterii fierului a atribuit hititilor din Anatolia monopolul tehnologiei fierului în epoca bronzului târziu. [25] . Această teorie nu mai este predată în programa școlară, [25] deoarece nu are dovezi istorice și arheologice. Deși au fost găsite unele obiecte de fier din Anatolia din epoca bronzului, numărul lor este comparabil cu cel al obiectelor de fier găsite în Egipt sau în alte locuri din aceeași perioadă și doar o mică parte din ele sunt arme. [24] În special în Asia Mică , regatele hitite din Anatolia s-au trezit separate de comerțul cu staniu: din acest motiv tribul Calibi a dezvoltat tehnica de carburare a fierului cu cărbune pentru a înlocui bronzul. Spre secolul al XIII-lea î.Hr., cultura orașului ilirilor s-a dezvoltat în Balcani , care a pus stăpânire pe toate staniile provenite din minele din Boemia , blocând aprovizionarea cu acest metal în Marea Egee . Acest lucru a provocat o criză economică gravă și, în consecință, invaziile Egiptului de către popoarele mării și războiul troian și, în cele din urmă, apariția epocii fierului în Mediterana . Unele surse speculează că fierul a fost inițial obținut folosind aceleași cuptoare care au fost utilizate pentru rafinarea cuprului . O teorie mai recentă a creșterii fierului se referă la prăbușirea imperiilor care la sfârșitul epocii târzii a bronzului a spulberat rutele comerciale necesare producției de bronz. [25] Disponibilitatea cuprului și chiar mai mult a staniului a fost redusă, ceea ce a necesitat transportul acestor materii prime pe distanțe mari. Se crede că la începutul epocii fierului transportul acestor materii prime nu era suficient pentru a satisface cererea celor care lucrau metalele. Acest lucru ar fi putut duce la utilizarea minereului de fier, care este mai abundent în natură decât minereurile de cupru și staniu. Deci creșterea fierului ar fi putut fi rezultatul unei nevoi, cauzată în principal de lipsa de staniu. De asemenea, în acest caz există o lipsă de dovezi arheologice care arată în special o lipsă de cupru sau staniu la începutul epocii fierului. [25] Obiectele din bronz sunt încă abundente și aceste obiecte au același procent de staniu ca și cele din epoca bronzului târziu.
Mesopotamia se afla deja la mijlocul epocii fierului în 900 î.Hr. , Europa Centrală în 800 î.Hr. Egiptul , pe de altă parte, nu a cunoscut o tranziție atât de rapidă din epoca bronzului în epoca fierului. Egiptenii au produs obiecte de fier, bronzul a rămas răspândit până la cucerirea Egiptului de către asirieni în 663 î.Hr.
Procesul de carburare
Contemporan la tranziția de la bronz la fier a fost descoperirea carburării (sau carburării ) sau procesul de îmbogățire a fierului maleabil superficial din carbon.
Fierul a fost obținut din minereul său în cuptoare alimentate cu cărbune a căror combustie a fost favorizată de suflarea aerului forțat produs de burduf . Monoxidul de carbon produs din cărbune a redus oxizii de fier la fierul metalic; aceasta a fost colectată sub forma unei mase spongioase sau a unei flori , ai cărei pori conțineau carbon și / sau carburi (provenind din cenușă) și zgură. Floarea a trebuit apoi încălzită din nou pentru a o bate și a expulza deșeurile încă închise în ea (majoritatea fragmente de cărbune și / sau minerale și o parte din carbon). A obținut fier maleabil care nu era întărit și o parte din oțel pe care ochiul practicantului a știut să o recunoască. Oamenii din Orientul Mijlociu au descoperit că se poate crea un fier mult mai dur încălzindu-l mult timp într-o coajă de praf de cărbune, transformând stratul de suprafață al materialului în oțel, apoi întărit.
Swords Damasc (oțel creuzet)

La scurt timp după anul o mie , tehnica indiană Wootz ajunge în Orientul Mijlociu , care până atunci importase pachete de oțel din Europa , unde este rafinat și dă naștere oțelului Damasc extrem de rezistent și flexibil cu care au fost forjate săbiile. care s-au confruntat cu cruciații europeni. Calitatea acestor arme a fost atât de ridicată încât s-a spus că o sabie din oțel Damasc ar putea tăia piatră și ar putea fi înfășurată în jurul unui om și apoi să se întoarcă drept ca înainte și să nu-și piardă niciodată marginea. După toate probabilitățile, tehnica Wootz a fost rafinată pentru a absorbi carbonul în special la marginile sabiei, păstrând miezul central relativ dulce. În acest fel, s-a obținut o sabie flexibilă care să reziste șocurilor fără a se rupe, dar în același timp cu o lamă foarte dură și păstrând o margine ascuțită mult timp (care în Europa , până în secolul al X-lea , a fost obținută prin montarea cele două fire de oțel separate foarte dure de pe lamă, deja pliate de mai multe ori și au lucrat până la forma finală). [26] Variațiile conținutului de carbon dintre margine și centrul sabiei au creat un model ondulat frumos la suprafață, de unde și adjectivul damasc . Nu s-au primit documente sau mărturii despre modul de obținere a oțelului din Damasc; [27] Pentru o vreme s-a crezut că oțelul Damasc nu era altceva decât un tip de oțel pachet , care în anumite condiții poate prezenta granule de suprafață, dar o comparație cu artefactele din oțel Damasc supraviețuitoare prezintă diferențe substanțiale, deși uneori chiar și oțelul Damasc arată urme de ambalare.
India
Siturile arheologice din India, cum ar fi Malhar , Dadupur, Raja Nala Ka Tila și Lahuradewa din Uttar Pradesh din prezent prezintă utilizări ale fierului în perioada cuprinsă între 1800 î.Hr și 1200 î.Hr. [28]
Cele mai vechi obiecte de fier găsite în India pot fi datate în 1400 î.Hr. folosind metoda de datare radioactivă a carbonului. Știfturi, cuțite , pumnal , vârfuri de săgeți , boluri , linguri , tigăi , topoare , dalte , clești, balamale de ușă etc. variind de la 600 î.Hr. până la 200 î.Hr. au fost găsite în mai multe situri arheologice indiene. [29] Unii cercetători cred că la începutul secolului al XIII-lea î.Hr. , producția de fier se practica pe scară largă în India, sugerând că data descoperirii tehnologiei poate fi anticipată. [28] În sudul Indiei (numit acum Mysore ) , există descoperiri de oțel , datând din secolul al 11 - lea î.Hr. la secolul al 12 - lea î.Hr. [30] Începutul 1st mileniu î.Hr. fierăstrău multe progrese în metalurgia fierului în India. Progresele tehnologice și stăpânirea metalurgiei au fost realizate în această perioadă de colonizare pașnică. [30] Anii care au urmat au cunoscut mai multe transformări ale tehnicilor metalurgice în perioada stabilă politic a Imperiului Maurya. [31]
Istoricul grec Herodot a dat prima înregistrare scrisă occidentală a utilizării fierului în India. [29] În textele religioase indiene (numite Upaniṣad ) există referiri la industria textilă, ceramică și metalurgică. [32]
Oțel Wootz
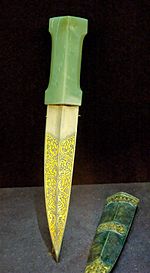
Prima metodă de producere a oțelului propriu-zis (adică oțel de înaltă calitate) a fost „Wootz”, similar cu metoda creuzetului modern, utilizată în sudul Indiei cel puțin din 300 d.Hr. (dar unii îl urmăresc până în 200 î.Hr. ); numele său este versiunea anglicizată a numelui hindus pentru oțel ( urukku ). A fost preparat în creuzete sigilate sigilate, care conținea minereu de fier de înaltă puritate, cărbune și sticlă . Creuzetele au fost apoi puse pe flacără și încălzite până când amestecul s-a topit, prin care fierul s-a îmbogățit cu carbon, iar sticla a absorbit impuritățile pe măsură ce s-a topit, plutind pe suprafață. [33] Rezultatul a fost un oțel cu un conținut ridicat de carbon, cu o puritate ridicată, denumit ulterior oțel Damasc .
Această tehnică s-a răspândit foarte încet, ajungând în țările vecine ( Turkmenistanul și Uzbekistanul de azi) abia în anul 900 d.Hr. Cuptorul din oțel din Damasc era un cuptor cu vânt, care folosea vânturile musonice pentru funcționarea sa. [33]
Oțelul Damasc este, de asemenea, renumit pentru rezistența sa și capacitatea de a ține firul. Era un aliaj complex, care avea fierul ca componentă principală. Studii recente au sugerat că nanotuburile de carbon (produse inconștient în proces) au fost incluse în structura sa, ceea ce ar putea explica caracteristicile sale mecanice. [34]
Lanțurile de fier au fost folosite de indieni pentru construirea podurilor suspendate înainte de secolul al IV-lea . [35]
Coloana de fier, care se află în complexul Qutba Delhi , capitala Indiei, este una dintre cele mai vechi curiozități metalurgice din lume. Stâlpul (înălțime de aproape șapte metri și greutate de peste șase tone) a fost ridicat de Chandragupta II Vikramaditya. [36] Stâlpul are un conținut de fier de 98%, dar a rezistat coroziunii în ultimii 1.600 de ani, contracarând condițiile meteorologice nefavorabile datorită conținutului ridicat de fosfor. Tehnica indiană a durat mult până a ajunge în Europa. Începând cu secolul al XVII-lea, olandezii au adus oțelul Damasc din sudul Indiei în Europa, unde ulterior și-a început producția pe scară largă, sub denumirea de tehnica creuzetului . [37]
Will Durant scrisse nel suo The Story of Civilization I: Our Oriental Heritage ("La storia della civiltà I: La nostra eredità Orientale"):
«Qualcosa è stato detto sull'eccellenza chimica della ghisa nell'India antica, e sull'elevato sviluppo industriale del periodo Gupta , quando l'India veniva vista, perfino dalla Roma imperiale , come la più abile delle nazioni in diversi tipi di industria chimica, come quella dei coloranti, della concia , della fabbricazione del sapone , del vetro e del cemento ... Dal sesto secolo gli Hindu erano molto più avanti dell'Europa nell'industria chimica; erano maestri della calcinazione , della distillazione , della sublimazione , della cottura a vapore , della fissazione, della produzione della luce senza calore , la preparazione di anestetici e polveri soporifere e della preparazione di sali metallici , composti e leghe . La tempra dell'acciaio in India fu portata a una perfezione sconosciuta in Europa fino ai nostri tempi; si dice che il Raja Puru abbia scelto, come dono speciale da Alessandro Magno non oro o argento, ma 30 libbre di acciaio. I musulmani portarono molta di questa scienza e industria Hindu nel Vicino Oriente e in Europa ; i segreti della fabbricazione delle lame di "Damasco" , per esempio, vennero presi dagli arabi dai Persiani , e questi ultimi li presero dall'India.» |
Cina
I primi sviluppi in Cina

Anche in Cina il primo ferro usato fu di origine meteorica. Manufatti di ferro battuto compaiono in siti archeologici datati attorno all' VIII secolo aC nel nord-ovest, vicino a Xinjiang . Questi pezzi sono stati fatti con le stesse tecniche in uso nel Medio Oriente ed in Europa . La produzione di acciaio, benché presente, soprattutto per la produzione di armi, era limitata. Negli ultimi anni della dinastia Zhou (attorno all'anno 550 aC ), nello Stato meridionale di Wu si sviluppò un'avanzata tecnologia basata su forni a torre, rastremati alla base, in grado di produrre ghisa in grandi quantità. [38] [39] [40] Alla loro temperatura di esercizio, anche più di 1.200 °C il ferro si combina con il 4,3% di carbonio e fonde ed è colato in stampi . Scaldando minerali di ferro con carbone a 1.200-1.300 °C si forma ghisa liquida, che è una lega di ferro al 96,5% e carbonio al 3,5%. Questa lega è troppo fragile per essere lavorata (in particolare è inadatta per impieghi da impatto), a meno che non venga decarburata per rimuovere la maggior parte del carbonio. La ghisa quindi veniva colata in stampi e decarburata fino allo stato di ferro dolce, arroventandola in focolari aperti per diversi giorni.
In Cina, questi metodi di lavorazione del ferro si diffusero a nord, e nel 300 aC il ferro era il materiale maggiormente impiegato per la produzione di attrezzi e di armi. Una grande tomba nella provincia di Hebei (datata all'inizio del III secolo aC ) contiene diversi soldati sepolti con le loro armi ed altro equipaggiamento. I manufatti recuperati da questa tomba sono fatti di ferro battuto, di ghisa, ghisa malleabile e acciaio temprato, con alcune armi di bronzo, probabilmente ornamentali. Il ferro rimase un prodotto poco pregiato, usato dai contadini per secoli e non interessò le classi nobiliari fino alla Dinastia Han ( 202 aC – 220 dC ), durante la quale la lavorazione del ferro cinese (più propriamente della ghisa) raggiunse una scala ed una sofisticazione elevatissime. Nel primo secolo , il governo Han fece diventare la lavorazione del ferro un monopolio di Stato e fece costruire una serie di grandi forni nella provincia di Henan , ognuno capace di produrre diverse tonnellate di ghisa al giorno. In questa epoca, i metallurgi cinesi scoprirono come impastare la ghisa grezza fusa rimescolandola all'aria aperta fino a che non avesse perso il carbonio e non fosse divenuta ferro malleabile (in lingua cinese il processo veniva chiamato chao , letteralmente saltato e fritto ). Nel I secolo aC , i metallurgi cinesi scoprirono che il ferro e la ghisa potevano essere saldati assieme per formare una lega con contenuto intermedio di carbonio, che era acciaio . [41] [42] [43] Secondo una leggenda, la spada di Liu Bang , il primo imperatore Han, fu creata con questa tecnica [ senza fonte ] . Alcuni testi del tempo menzionano l' armonizzazione del duro e del morbido nel contesto della lavorazione del ferro; la frase potrebbe riferirsi a questo processo. Inoltre, la città antica di Wan ( Nanyang ) del periodo Han precedente era un grosso centro manifatturiero di ferro e acciaio. [44] Assieme ai loro metodi originali per forgiare l'acciaio, i cinesi hanno anche adottato i metodi di produzione per creare l' acciaio Damasco , un'idea importata dall' India alla Cina nel V secolo dC [45]
La tecnologia cinese degli altiforni (o acciaio al crogiolo ) e del pudellaggio fu ripresa in Europa nel tardo Medioevo .
I mantici ad acqua cinesi

I cinesi durante l'antica Dinastia Han furono anche i primi ad applicare l'energia idraulica (da un mulino ad acqua) per fare funzionare i mantici di una fornace. Questo fu annotato nell'anno 31 dC, come innovazione dell' ingegnere Du Shi , del prefetto di Nanyang. [46] Dopo Du Shi, i cinesi continuarono a utilizzare l'energia dell'acqua per muovere i mantici delle fornaci. Nel testo del Wu Chang Ji del V secolo il suo autore Pi Ling scrisse che un lago artificiale fu progettato e costruito nel periodo del regno di Yuan-Jia ( 424 – 429 ) per il solo scopo di alimentare le ruote dei mulini aiutando i processi di fusione e stampaggio dell'industria del ferro cinese. [47] Il testo del V secolo Shui Jing Zhu menziona l'uso dell'acqua corrente di fiume per alimentare i mulini, come ne parla il testo geografico dello Yuan.he Jun Xian Tu Chi della Dinastia Tang , scritto nell' 814 dC [48]
Ci sono prove che la produzione dell'acciaio nell' XI secolo nella Cina dei Song avvenisse usando due tecniche: un medodo "berganesque", che produceva un acciaio inferiore e disomogeneo e un precursore al moderno processo Bessemer , che utilizzava una decarburizzazione parziale attraverso forgiature ripetute sotto un soffio freddo. [49] Nell'XI secolo ci fu anche una grossa deforestazione in Cina, a causa delle richieste di carbone dell'industria siderurgica. [50] In questo periodo i cinesi scoprirono come usare il carbon coke al posto del carbone vegetale. [50] L'introduzione del carbone minerale al posto del carbone vegetale si ebbe poi in Europa nel XVII secolo.
Anche se Du Shi fu il primo a utilizzare l'energia idraulica per alimentare i mantici nella metallurgia, la prima illustrazione disegnata ed illustrata di questa alimentazione idraulica risale al 1313 , nel testo dell'era della Dinastia Yuan chiamato Nong Shu . [47] Il testo fu scritto da Wang Zhen ( 1290 - 1333 dC), che così spiegò i metodi usati per l'altoforno con mantici alimentati ad acqua nei periodi precedenti la sua era del XIV secolo :
«"In accordo con gli studi moderni (+1313!), i mantici con sacco in cuoio (wei nang) erano usati ai vecchi tempi, ma ora vengono usati sempre dei ventagli in legno. Il design è il seguente. Viene scelto un luogo vicino a un forte torrente, e un palo viene innalzato verticalmente in una struttura con due ruote orizzontali in modo da avere quella più in basso spinta dalla forza dell'acqua. La più alta è collegata con una cinghia a una ruota (più piccola) davanti ad essa, la quale ha un manico eccentrico (letteralmente un ingranaggio oscillante). Poi vi è un blocco, che segue la rotazione (della ruota principale), con un ingranaggio collegato al manico eccentrico che tira e spinge il rullo oscillante, le leve a destra ea sinistra del quale assicurano la trasmissione del moto all'ingranaggio del pistone. Quindi questo viene spinto avanti e indietro, azionando i mantici della fornace molto più velocemente di quanto sarebbe possibile con la forza umana. [51] » |
«Viene usato anche un altro metodo. Alla fine del pistone in legno, lungo circa 3 piedi che viene fuori dalla parte frontale dei mantici, c'è un pezzo incurvato di legno con la forma della luna crescente, e (tutto) questo è sospeso in alto con una corda come quella di un'altalena. Poi, davanti ai mantici, ci sono (molle di) bambù collegate ad essi dalle corde; questo controlla il movimento del ventaglio dei mantici. Poi, seguendo la rotazione della ruota (verticale) del mulino, il manico collegato all'asse principale schiaccia e preme la tavola incurvata (collegata al pistone) che corrispondentemente si muove indietro (letteralmente "in dentro"). Quando il manico è finalmente disceso il bambù (le molle) agisce sui mantici e li riportano nella posizione iniziale. In maniera simile, usando un solo asse principale, è possibile attuare diversi mantici (con estensioni sull'asse), con lo stesso principio dei martelli a caduta ( shui tui ). Questo è anche molto conveniente e veloce... [51] » |
Giappone
Spade da samurai
In Giappone i costruttori di spade furono gelosi custodi delle loro tecniche di fabbricazione dell'acciaio usato per le spade da samurai .
La tecnica era (ed è ancora) simile a quella utilizzata per l'acciaio a pacchetto, ma con alcune differenze sostanziali: la lama veniva realizzata dividendo la battitura a strati prima su una parte esterna di acciaio più duro, destinata a divenire la parte esterna e il filo della lama, nella quale in seguito veniva parzialmente inserita una barra di acciaio più morbido che ne costituiva l'anima flessibile. La katana assumeva in tal modo, dopo la forgiatura , la tempra e la pulizia, un'estrema affilatura ed un'estrema flessibilità.
Europa
La ferriera alla genovese

Nella seconda metà del XIV secolo fece la sua comparsa nella Repubblica di Genova un nuovo modo di produrre il ferro in un impianto detto ferriera o ferrera alla genovese dai suoi stessi creatori. A partire dal XVI secolo essa è presente in tutti i paesi del Mediterraneo – dalla Sicilia al Piemonte, al Delfinato fino ai Paesi Baschi – e risulta aver soppiantato tutti quegli impianti a focolare chiuso – fornelli – da cui si ricavava un massello – blumo – contenente ferro carbone e acciaio da raffinare ulteriormente. La nuova tecnica utilizzava un solo impianto a focolare aperto, del tutto simile a quello utilizzato per la raffinazione della ghisa. Mantici mossi da ruota idraulica alimentavano la combustione di una miscela di minerale e carbone di legna potendo raggiungere una temperatura massima di 1.200 °C. Con la liquefazione della ganga si formava un blumo di ferro spugnoso grazie all'opera di rimescolamento eseguita da un pratico. Con successivi riscaldi e battiture al maglio idraulico il blumo raggiungeva la sua forma definitiva di barra di ferro. Agricola documenta impianti analoghi, ma senza un legame apparente con le ferriere alla genovese, nell'Alto Palatinato alla fine del Quattrocento. Il limite del processo era il dover disporre di un minerale ricco e facilmente fusibile – come è il caso delle ematiti elbane e pirenaiche – e nell'impossibilità di produrre direttamente acciaio. Il suo punto di forza era, oltre il basso impiego di manodopera e capitali, nella produzione di un ottimo ferro malleabile: un fatto di rilievo sia tecnico sia economico che prolungherà la sua esistenza fino alla prima metà dell'Ottocento. La ferriera alla genovese passa da una produzione nel Quattrocento di circa un quintale di ferro nelle 24 ore ai tre quintali (suddivisi in tre masselli) nel secolo successivo. Sul finire del Settecento e fino a metà Ottocento del termine alla genovese si perde la memoria e saranno rinomati gli impianti alla catalana francesi e spagnoli che migliorando il processo e usando magli particolarmente efficienti garantivano produzioni anche di 6 quintali nelle 24 ore. Se oggi si sfoglia un dizionario tecnico catalana è sinonimo di ferriera a riduzione diretta [52] .
L'acciaio a pacchetto
In Europa la principale tecnica utilizzata fino al X secolo fu quella dell'acciaio a pacchetto, che consentiva di controllare più agevolmente il tenore di carbonio del metallo rispetto a quanto si poteva fare usando l'acciaio omogeneo che pure veniva prodotto, in quantità limitate, dai bassoforni alto-medioevali.
Consiste nel creare un pacchetto di strati alternati di ferro dolce e ghisa , fatti rammollire e poi martellati insieme per saldarli e far diffondere il carbonio dalla ghisa al ferro dolce, in modo da ottenere la percentuale di carbonio desiderata. Una volta saldati gli strati del pacchetto, si taglia la barra e la si piega su sé stessa, ripetendo il processo: in questo modo si possono creare barre estremamente resistenti composte di centinaia o migliaia di strati sottilissimi. È un processo la cui riuscita dipende moltissimo dalla capacità e dall'esperienza del fabbro : è molto difficile ottenere due volte lo stesso risultato con questo metodo in quanto la lunghezza della lavorazione alla forgia, la sua complessità, così come il calore a cui viene riscaldato il pezzo in lavorazione, influenzano il tenore in carbonio dell'acciaio e le caratteristiche meccaniche del pezzo finito.
Il processo è noto in Europa fin dalla tarda epoca dei Celti (dopo che l'uso dei perfezionati bassoforni greci si era diffuso nell'Europa Occidentale), dei quali sono rimaste alcune spade che mostrano una stratificazione di questo genere (per quanto limitata a poche decine di strati). Alla fine dell'età romana era sicuramente noto ai barbari di stirpe germanica, ed è stato per secoli l'unico modo noto, al di fuori dell'India, per ottenere acciaio di buona qualità.
Per secoli l'unico modo di ottenere del buon acciaio in Europa fu quindi quello di usare ferro delle miniere svedesi , particolarmente puro e privo di zolfo e fosforo , "ferro di palude" ( limonite ), siderite di origine alpina o ematite dell' Isola d'Elba , ed usarlo per confezionare acciaio a pacchetto con ghisa più ricca di carbonio. Era un processo molto lento ed estremamente costoso: per un chilogrammo di acciaio erano necessari circa 100 kg di combustibile . Per questo non era conveniente creare pezzi più grandi di una lama di spada . In genere si usava l'acciaio per creare piccoli manufatti, come punte di freccia , bisturi , coltelli ed altri oggetti di piccole dimensioni.
Per questo motivo durante il basso Medioevo in Europa, all'incirca a partire dal IX secolo , con l'aumentata disponibilità di acciaio omogeneo, che riduceva i tempi di lavorazione, la tecnica dell'acciaio a pacchetto fu progressivamente abbandonata, portando a un generale scadimento della qualità delle lame europee del periodo. Dall' XI secolo al XVI secolo la tecnica cadde completamente in disuso. Venne riscoperta con il Rinascimento , data la maggiore richiesta di lame di qualità superiore e peso inferiore, e in quel periodo molti si convinsero che l'acciaio Damasco, di cui i crociati raccontavano meraviglie, non fosse altro che un tipo di acciaio a pacchetto, ma questa credenza è stata smentita dalle analisi delle nervature visibili nei due tipi di acciaio.
Il processo di "lavorazione a Damasco" è ancora oggi utilizzato per la produzione artigianale di coltelleria e repliche di armi bianche storiche di alta qualità.
I primi forni da ghisa in Europa
In Europa si cominciò a produrre ghisa per fare ferro e acciaio nel basso Medioevo quando furono costruiti forni chiusi con un particolare profilo a imbuto e grazie all'impiego della ruota idraulica ad asse orizzontale utilizzata per azionare i mantici; fu così relativamente facile ottenere e controllare temperature superiori ai 1200 °C (1147 °C temperatura di fusione dell' eutettico della ghisa). La ghisa ottenuta dal forno era rifusa in fucine , anch'esse di nuova concezione, che utilizzavano soffierie idrauliche particolarmente potenti, indispensabili per produrre le alte temperature (1200 °C) necessarie a liquefarla nuovamente per farne getti, ferro e acciaio. Le prime notizie di impianti con tali caratteristiche riguardano il Dalarne-Vestmanland nella Svezia centrale (datati al XIII secolo e poi detti masugn ), la Markisches Sauerland, nella Ruhr tedesca (forni da ghisa datati col radiocarbonio fra il 1205 e il 1300, prima menzione scritta Masshutte nel 1311) e il lato meridionale delle Alpi centrali ( furnus nel 1179 ad Ardesio e furnus e fuxina a Schilpario nel 1251 ea Semogo nel 1286) [53] .
Processi di affinamento
Un metodo alternativo di decarburizzare la ghisa grezza sembra essere stato ideato nella regione attorno a Namur nel XV secolo . Questo processo vallonico si diffuse alla fine del secolo fino al Pay de Bray , sul confine orientale della Normandia , e poi verso la Gran Bretagna , dove divenne il metodo principale per la fabbricazione del ferro battuto nel 1600 . Fu introdotto in Svezia da Louis de Geer all'inizio del XVII secolo e fu usato per fabbricare il ferro di Oreground (dal nome della cittadina Svedese di Öregrund ).
Una variazione di questo era il procedimento tedesco . Divenne il metodo principale per produrre il ferro battuto in Svezia .
L'acciaio Bulat
L'acciaio Bulat (dalla parola persiana pulad , acciaio) fu inventato da Pavel Petrovich Anosov , dopo anni di studi sulla perduta arte dell' acciaio Damasco di cui Anosov voleva riscoprire il segreto. L'acciaio Bulat era un acciaio stratificato, ottenuto raffreddando molto lentamente la massa fusa in modo che il carbonio si potesse concentrare in strati diversi: in questo modo il metallo finale consisteva di molti strati di ferrite (acciaio dolce) e perlite (acciaio duro).
La perlite però è instabile a temperature superiori a 727 °C e tende a scomporsi in ferrite e austenite, per trasformarsi di nuovo al raffreddamento, motivo per cui la lavorazione a caldo di questo tipo di acciaio richiedeva particolare attenzione.
L'acciaio cementato
All'inizio del XVII secolo , i siderurgisti nell'Europa Occidentale trovarono un modo (chiamato cementazione ) per carburare il ferro battuto. Le barre in ferro e il carbone venivano messi dentro scatole in pietra, poi mantenute a una temperatura rossa (la temperatura a cui il ferro diviene leggermente luminescente e "rosso") fino a una settimana. In questo periodo, il carbonio diffonde nel ferro, producendo un materiale chiamato acciaio cementato o acciaio a bolle . A Coalbrookdale , in Inghilterra , si trovano due fornaci per la cementazione utilizzate da Sir Basil Brooke , che tenne il brevetto sul processo tra il 1610 e il 1619.
La qualità dell'acciaio poteva essere migliorata lavorandolo tramite la piegatura su sé stesso, producendo acciaio a strati. Tuttavia nel periodo tra il 1740 e il 1750 Benjamin Huntsman trovò un modo di fondere nei crogioli l'acciaio cemento ottenuto dal processo di cementazione.
Sviluppo delle fonderie alimentate idraulicamente
A volte, nel periodo medioevale, l'energia dell'acqua era applicata ai processi delle fonderie. È possibile che questo avvenne presso l' Abbazia di Clairvaux dell' Ordine Cisterciense nel 1135 , ma fu certamente in uso in Francia e in Svezia all'inizio del XIII secolo . [54] In Inghilterra , le prime chiare prove documentate di questo furono nella contabilità di una forgia del Vescovato di Durham , vicino a Bedburn nel 1408 , [55] ma non fu certamente la prima volta che venivano impiegate simili tecniche siderurgiche. Nel distretto inglese di Furness , le fonderie alimentate idraulicamente furono in uso all'inizio del XVIII secolo , e vicino a Garstang fino al 1770 circa.
La forgia catalana è un tipo di fonderia alimentata. Le fonderie con il "soffio caldo" erano usate nello Stato di New York a metà del XIX secolo .
L'invenzione del carbon coke
Fondamentale fu l'introduzione del coke , avvenuta nel Settecento in Inghilterra . "Cuocendo" il carbone (ovvero scaldandolo in assenza di ossigeno ) si otteneva carbone "cooked" o coke . Il coke venne utilizzato negli altoforni al posto del carbone di legna, permettendo di incrementare la produzione di ghisa grezza.
Le prime fusioni del ferro usavano il carbone vegetale sia come sorgente di calore che come agente di riduzione. Nel XVIII secolo la disponibilità di legno per il carbone limitava l'espansione della produzione del ferro e l'Inghilterra divenne sempre più dipendente, per una parte considerevole del ferro richiesto dalle sue industrie, dalla Svezia (dalla metà del XVII secolo ) e poi dal 1725 anche dalla Russia . [56]
La fusione tramite carbon fossile (o il suo derivato carbon coke ) era un obiettivo cercato da tempo. La produzione della ghisa grezza con il coke fu probabilmente ottenuta da Dud Dudley nel 1620 , e con un mix di carburanti fatto con carbon fossile e legno nel 1670 . Questo fu però probabilmente soltanto un successo tecnologico e non commerciale. Shadrach Fox potrebbe aver fuso il ferro con il coke presso Coalbrookdale in Shropshire nel 1690 , ma soltanto per fare palle di cannone ed altri prodotti in ghisa come gusci. Tuttavia, nella pace seguita alla guerra dei nove anni , non ci fu una sufficiente domanda di queste. [57]
Abraham Darby ei suoi successori
Nel 1707 , Abraham Darby I brevettò un metodo per la fabbricazione di pentole in ghisa; tali pentole erano più sottili e quindi più economiche di quelle della concorrenza. Avendo bisogno di una quantità maggiore di ghisa grezza, egli noleggiò l' altoforno di Coalbrookdale nel 1709. Là, egli fabbricò il ferro utilizzando il coke , stabilendo di conseguenza il primo commercio di successo di questo genere in Europa. Lo sviluppo del suo metodo che prevedeva di caricare il forno con coke e minerale di ferro, porterà alla tecnologia degli altoforni alimentati a coke che tuttora è quella utilizzata. I suoi prodotti erano tutti in ghisa , anche se i suoi successori più immediati tentarono (con piccolo successo commerciale) di affinarlo in ferro (puro) in barre. [58]
Il ferro in barre continuò di conseguenza ad essere fabbricato con ghisa grezza al carbone vegetale fino al 1755 . In questo anno Abraham Darby II (e soci) aprirono una nuova fornace funzionante con il coke presso Horsehay in Shropshire e fu presto imitato da altri. Questi procurarono ghisa grezza al coke alle forge di affinatura di tipo tradizionale per la produzione di ferro battuto. La ragione di questo ritardo rimane controversa [59] anche se probabilemnete dovuta ad una serie di cause. In effetti, almeno inizialmente il coke presentava un costo maggiore del carbone vegetale e lasciava nella ghisa un eccesso di silicio rendendola di cattiva qualità [60] ed altre difficoltà tecniche che necessitarono di tempo per essere risolte.
La reinvenzione dell'acciaio al crogiolo
Nel 1740 Benjamin Huntsman , a Sheffield , riscoprì la tecnica dell'acciaio al crogiolo. Dopo anni di esperimenti in segreto, mise a punto una fornace in grado di raggiungere i 1600 °C in cui metteva una dozzina di crogioli di argilla , ciascuno con 15 kg di ferro, che veniva portato lentamente al calor bianco; a questo punto si aggiungevano pezzi di ghisa, i quali, lasciati fondere, aggiungevano al materiale il carbonio necessario; dopo tre ore circa l'acciaio fuso veniva colato in lingotti.
Nel 1740 Sheffield produceva circa 200 tonnellate di acciaio all'anno; un secolo dopo ne produceva 80.000, la metà di tutta la produzione europea, ed era la più grande città industriale d'Europa.
Questo modo di produrre l'acciaio dominò fino all'arrivo del convertitore Bessemer , che produceva acciaio di qualità comparabile ma con costi minori.
Nuovi processi di forgiatura
Fu soltanto dopo questi avvenimenti che cominciarono ad essere concepiti modi attuabili economicamente per convertire la ghisa grezza in ferro. Un processo conosciuto come invasatura e stampaggio fu ideato nel 1760 e migliorato nel 1770, e sembra essere stato ampiamente adottato nelle Midlands occidentali circa dal 1785 . Tuttavia, questo metodo fu rimpiazzato dal processo di affinatura di Henry Cort , brevettato nel 1784 , ma probabilmente fatto funzionare con ghisa grezza grigia circa nel 1790 . Questi processi permisero la grande espansione della produzione del ferro che costituì la Rivoluzione industriale per l'industria del ferro. [61]
All'inizio del XIX secolo , Hall scoprì che l'aggiunta di ossidi di ferro al contenuto dei forni di affinatura provocava una violenta reazione, nella quale la ghisa grezza veniva decarburizzata; questo processo venne chiamato 'affinatura umida'. Si scoprì anche che era possibile produrre acciaio fermando il processo di affinatura prima che la decarburizzazione fosse completa.
Vento caldo
L'efficienza dell' altoforno fu migliorata dall'innovazione del "vento caldo" (l'aria, prima di entrare nella fornace, veniva preriscaldata), brevettato da James Beaumont Neilson in Scozia nel 1828 . Questo ridusse ulteriormente i costi di produzione. Nel giro di pochi decenni, l'abitudine divenne quella di avere una 'stufa' grande quanto la fornace vicino ad essa, nella quale i gas d'altoforno (contenenti CO, monossido di carbonio) provenienti dalla fornace venivano diretti e bruciati. Il calore risultante veniva usato per preriscaldare l'aria soffiata nella fornace. [62]
Il forno Martin-Siemens
Negli anni 1850 Sir Carl Wilhelm Siemens ideò il cosiddetto forno Siemens, che rispetto alle metodologie precedenti riusciva a diminuire i consumi di combustibile del 70-80%.
Nel 1865 l'ingegnere francese Pierre-Emile Martin acquistò il brevetto e introdusse l'uso del forno Siemens (che da quel momento in poi fu chiamato "forno Martin-Siemens") per svolgere l'ossigenazione della ghisa grezza (in inglese pig iron ).
L'invenzione del convertitore
A parte una qualche produzione di acciaio affinato, l'acciaio Inglese continuò ad essere fabbricato tramite cementazione, a volte seguita da rifusione per produrre acciaio in crogiolo. Questi erano processi "in lotto" la cui materia prima era il ferro (puro) in barre, in particolare il ferro di Oregrund in Svezia .
Il problema della produzione in massa di acciai economici fu risolto nel 1855 da Henry Bessemer , con l'introduzione del convertitore Bessemer nella sua fabbrica di Sheffield in Inghilterra . [63] Nel convertitore Bessemer, la ghisa grezza fusa proveniente dall'altoforno veniva inserita in un grosso crogiolo e poi veniva soffiata aria dal basso attraverso il materiale fuso, bruciando il carbonio disciolto dal coke. Mano a mano che il carbonio brucia, il punto di fusione del materiale aumenta, ma il calore proveniente dal carbonio in fiamme procura l'energia in più necessaria a mantenere il miscuglio fuso. Dopo che il contenuto in carbonio nella colata ha raggiunto il livello desiderato, il flusso d'aria può essere chiuso. Un tipico convertitore Bessemer poteva convertire un lotto di 25 tonnellate di ghisa grezza in acciaio in mezzora circa. L'invenzione dei convertitori ad aria, primo fra i quali il convertitore Bessemer , permise di abbandonare il metodo del pudellaggio (acciaio al crogiolo), lungo e dispendioso.
L'acciaio inox
Vi furono innumerevoli tentativi svolti nel XIX secolo, tesi ad ottenere una lega che mantenesse le caratteristiche meccaniche dell'acciaio risultando però inossidabile. Le varie sperimentazioni si orientarono verso l'aggiunta nell'acciaio di cromo , nichel ed altri metalli [64] . Nel 1913 l'inglese Harry Brearly riuscì ad ottenere effettivamente l' acciaio inossidabile mediante un'alta percentuale di cromo. [65]
I convertitori a ossigeno
Nel 1952 venne poi introdotto alla Voest-Alpine il processo di ossigenazione, [66] [67] una modifica al processo Bessemer, che lancia ossigeno da sopra all'acciaio (invece che soffiare aria da sotto), riducendo la quantità di azoto incluso nell'acciaio. Questo processo viene usato in tutte le fabbriche di acciaio attuali; l'ultimo convertitore Bessemer degli Stati Uniti venne messo a riposo nel 1968 . Inoltre, a partire dagli anni seguenti la seconda Guerra Mondiale, a Brescia (Italia), utilizzando solo rottami di ferro fusi nel forno elettrico ad arco , iniziarono a produrre acciaio dei piccoli stabilimenti chiamati ironicamente mini-acciaierie. Queste fabbriche producevano solo prodotti in barre all'inizio, ma si sono poi espansi a prodotti piatti e pesanti, una volta dominio esclusivo dei circuiti della fabbricazione dell'acciaio integrata.
Prima di questi sviluppi del XIX secolo , l'acciaio era un lusso costoso e veniva usato solo per un numero limitato di scopi nei quali era necessario un metallo particolarmente duro o flessibile, come nelle parti taglienti degli attrezzi e nelle molle. La grande diffusione di acciaio poco costoso alimentò la seconda rivoluzione industriale e la società moderna come la conosciamo. L'acciaio dolce ha rimpiazzato il ferro battuto per quasi tutti gli scopi, e quest'ultimo non viene più (o quasi più) fabbricato. Con piccole eccezioni, le leghe di acciaio cominciarono ad essere prodotte solo nel tardo XIX secolo. L' acciaio inossidabile fu sviluppato solo all'alba della prima guerra mondiale e divenne largamente usato soltanto negli anni 1920 . Queste leghe di acciaio sono tutte conseguenza della grande disponibilità di ferro ed acciaio a basso costo e della possibilità di legarli a volontà.
Nel 1992 il processo Martin-Siemens era definitivamente soppiantato negli Stati Uniti d'America dai convertitori a ossigeno (come il convertitore Bessemer e il processo Linz-Donawitz [68] ). La nazione con la percentuale più alta di acciaio prodotto a mezzo del processo Martin-Siemens (circa il 50%) rimane l' Ucraina . [69]
Note
- ^ Archeometallurgia del ferro
- ^ L'aggettivo "ponderale" fa riferimento al termine " concentrazione in massa " o "percentuale in massa", con il quale si indica la concentrazione espressa dal rapporto tra la massa del componente in miscela e la massa totale della miscela, moltiplicato per 100.
- ^ Enzo Baraldi, Una nuova età del ferro: macchine e processi della siderurgia , in Il Rinascimento italiano e l'Europa , Volume III: Produzioni e tecniche , Treviso, Angelo Colla editore, 2007. ISBN 978-88-89527-17-7 .
- ^ Duncan E. Miller and NJ Van Der Merwe, "Early Metal Working in Sub Saharan Africa" in Journal of African History 35 (1994) 1-36; Minze Stuiver and NJ Van Der Merwe, "Radiocarbon Chronology of the Iron Age in Sub-Saharan Africa" in Current Anthropology 1968.
- ^ Storia della chimica e della scienza. Biografie di scienziati. Bessemer , su minerva.unito.it . URL consultato il 26 marzo 2009 (archiviato dall' url originale l'8 agosto 2010) .
- ^ Copia archiviata ( PDF ), su museoitalianoghisa.org . URL consultato il 26 marzo 2009 (archiviato dall' url originale il 17 giugno 2012) .
- ^ Benvéniste 1969 cit. dep; Rick Mc Callister and Silvia Mc Callister-Castillo, Etruscan Glossary , su etruscans1.tripod.com , 1999. URL consultato il 19 giugno 2006 .
- ^ Online etymology dictionary , su etymonline.com .
- ^ myEtymology.com: English etymology of iron
- ^ IF 46:184f
- ^ "Pietre cadute dal cielo" - Meteoriti al Planetario di Torino Archiviato il 15 febbraio 2009 in Internet Archive .
- ^ RF Tylecote, A History of Metallurgy (2nd edn, 1992), 3
- ^ Meteoriti Archiviato il 19 ottobre 2012 in Internet Archive .
- ^ Girolamo Zampieri, "Bronzi antichi" , L'erma di Bretschneider editore, 2000, ISBN 88-8265-117-7 p.113
- ^ TA Rickard , The Use of Meteoric Iron , in The Journal of the Royal Anthropological Institute of Great Britain and Ireland , vol. 71, n. 1/2, 1941, pp. 55–66., DOI : 10.2307/2844401 .
- ^ Buchwald, VF, On the Use of Iron by the Eskimos in Greenland , in Materials Characterization , vol. 29, n. 2, 1992, pp. 139–176, DOI : 10.1016/1044-5803(92)90112-U .
- ^ Meteoritical Bulletin, no. 28, Moscow (1963)
- ^ Anatomia nell'Iliade di Omero
- ^ "Iliade di Omero", traduzione di Vincenzo Monti
- ^ Monica Pugliara, "Il mirabile e l'artificio"
- ^ E. Photos, "The Question of Meteoritic versus Smelted Nickel-Rich Iron: Archaeological Evidence and Experimental Results" World Archaeology Volume 20, Numero 3, Archaeometallurgy (febbraio 1989), pp. 403-421.
- ^ Waldbaum, Jane C. From Bronze to Iron. Göteburg: Paul Astöms Förlag (1978): 56-8.
- ^ Breve storia del Ferro , su zoomedia.it .
- ^ a b Waldbaum 1978: 23.
- ^ a b c d Muhly, James D. 'Metalworking/Mining in the Levant' pp. 174-83 in Near Eastern Archaeology ed. S. Richard Winona Lake, IN: Eisenbrauns (2003): 180.
- ^ Cosa è l'acciaio damascato
- ^ Comi Ivano , "Acciaio Damasco", 1996, Hoepli editore. ISBN 88-203-2297-8
- ^ a b The origins of Iron Working in India: New evidence from the Central Ganga plain and the Eastern Vindhyas by Rakesh Tewari (Director, UP State Archaeological Department)
- ^ a b Marco Ceccarelli (2000). International Symposium on History of Machines and Mechanisms: Proceedings HMM Symposium . Springer. ISBN 0-7923-6372-8 . pp 218
- ^ a b IM Drakonoff (1991). Early Antiquity . University of Chicago Press. ISBN 0-226-14465-8 . pp 372
- ^ JF Richards et al (2005). The New Cambridge History of India . Cambridge University Press. ISBN 0-521-36424-8 . pp 64
- ^ Patrick Olivelle (1998). Upanisads . Oxford University Press. ISBN 0-19-283576-9 . pp xxix
- ^ a b G. Juleff, An ancient wind powered iron smelting technology in Sri Lanka , in Nature , vol. 379, n. 3, 1996, pp. 60-63, DOI : 10.1038/379060a0 .
- ^ Katharine Sanderson, Sharpest cut from nanotube sword: Carbon nanotech may have given swords of Damascus their edge , Nature , 15 novembre 2006. URL consultato il 17 novembre 2006 .
- ^ Suspension bridge. (2007). In Encyclopedia Britannica. Retrieved April 5, 2007, from Encyclopedia Britannica Online
- ^ Delhi Iron Pillar: New Insights . R. Balasubramaniam, Delhi: Aryan Books International and Shimla: Indian Institute of Advanced Studies, 2002, Hardbound, ISBN 81-7305-223-9 . Review: Delhi Iron Pillar: New Insights LIST OF PUBLICATIONS ON INDIAN ARCHAEOMETALLURGY
- ^ Roy Porter (2003). The Cambridge History of Science . Cambridge University Press. ISBN 0-521-57199-5 . pp 684
- ^ Needham, Volume 4, Part 2, 544 g
- ^ Woods, 49-50.
- ^ Wagner, 52.
- ^ Needham, Volume 4, Part 3, 197.
- ^ Needham, Volume 4, Part 3, 277.
- ^ Needham, Volume 4, Part 3, 563 g
- ^ Needham, Volume 4, Part 3, 86.
- ^ Needham, Volume 4, Part 1, 282.
- ^ Needham, Volume 4, Part 2, 370
- ^ a b Needham, Volume 4, Part 2, 371-372.
- ^ Needham, Volume 4, Part 2, 373.
- ^ Robert Hartwell, 'Markets, Technology and the Structure of Enterprise in the Development of the Eleventh Century Chinese Iron and Steel Industry' Journal of Economic History 26 (1966). pp. 53-54
- ^ a b Ebrey, 158.
- ^ a b Needham, Volume 4, Part 2, 376.
- ^ Enzo Baraldi, La “ferriera alla genovese” tra XIV e XVII secolo , in: Pratiche e Linguaggi. Contributi a una storia della cultura tecnica e scientifica , Edizioni ETS 2005
- ^ Enzo Baraldi, Una nuova età del ferro: macchine e processi della siderurgia , in Il Rinascimento italiano e l'Europa , Volume III: Produzioni e tecniche , Treviso, Angelo Colla editore, 2007. ISBN 978-88-89527-17-7
- ^ AR Lucas, 'Industrial milling in the ancient and Medieval Worlds' Technology and Culture 46 (2005), 19.
- ^ RF Tylecote, A History of Metallurgy , 76.
- ^ PW King, 'The production and consumption of bar iron in early modern England and Wales' Economic History Review 58(1) (2005), 1-33.
- ^ PW King, 'Dud Dudley's contribution to metallurgy' Historical Metallurgy 36(1) (2002), 43-53; PW King, 'Sir Clement Clerke and the adoption of coal in metallurgy' Trans. Newcomen Soc. 73(1) (2001-2), 33-52.
- ^ A. Raistrick, A dynasty of Ironfounders (1953; 1989); N. Cox, 'Imagination and innovation of an industrial pioneer: The first Abraham Darby' Industrial Archaeology Review 12(2) (1990), 127-144.
- ^ A. Raistrick, Dynasty ; CK Hyde, Technological change and the British iron industry 1700-1870 (Princeton, 1977), 37-41; PW King, 'The Iron Trade in England and Wales 1500-1815' (Ph.D. thesis, Wolverhampton University, 2003), 128-41.
- ^ S. Ciriacono, La rivoluzione industriale: dalla protoindustrializzazione alla produzione flessibile , 2000
- ^ GR Morton and N. Mutton, 'The transition to Cort's puddling process' Journal of Iron and Steel Institute 205(7) (1967), 722-8; RA Mott (ed. P. Singer), Henry Cort: The great finer: creator of puddled iron (1983); PW King, 'Iron Trade', 185-93.
- ^ A. Birch, Economic History of the British Iron and Steel Industry , 181-9; CK Hyde, Technological Change and the British iron industry (Princeton 1977), 146-59.
- ^ Uno dei primi convertitori è ancora visibile presso il Kelham Island Museum nella città.
- ^ G.Di Caprio, Gli acciai inossidabili , 2003
- ^ http://www.mbmitalia.com/new/userimages/AcciaioStoria.pdf
- ^ In inglese è chiamato Basic oxygen steelmaking (BOS), Basic Oxygen Furnace (BOF), Linz-Donawitz-Verfahren , o LD-converter .
- ^ McGannon, Harold E. editore (1971). The Making, Shaping and Treating of Steel: Ninth Edition . Pittsburgh, Pennsylvania: United States Steel Corporation , p.26
- ^ Detto anche "Processo LD".
- ^ 41724.PDF ( PDF ), su energystar.gov . URL consultato il 4 maggio 2019 (archiviato dall' url originale il 9 agosto 2017) .
Bibliografia
- Ernesto Salamoni, Dal ferro all'acciaio , Editori Riuniti, 1994, ISBN 88-359-2576-2 .
- Mauro Cavallini, Fortuitum & sordidum opus. Appunti di storia della metallurgia , CRACE, 2005, ISBN 88-87288-58-5 .
- Andrea Raggi, Barbara Paparo, Giancarlo Barbiroli, Mutamenti tecnologici e strutturali nell'industria siderurgica mondiale. Un modello altamente innovativo , 2ª ed., Edizioni Franco Angeli, 2000, ISBN 88-464-0046-1 .
- Massimo Paoli, Struttura e progresso tecnologico della industria siderurgica. Il caso italiano , 1ª ed., Edizioni Franco Angeli, 1984, ISBN 88-204-4163-2 .
- Angelo Nesti, La siderurgia toscana nel XVIII secolo , Felici Editore, 2005, ISBN 88-88327-97-5 .
- Bay Fernand, Paesaggi industriali del Novecento. Siderurgia e miniere nella Maremma Toscana. , a cura di Massimo Preite, Polistampa Editore, 2006, ISBN 88-596-0140-1 .
- ( EN ) Patricia Buckley Ebrey, Anne Walthall, James B. Palais, East Asia: A Cultural, Social, and Political History , 1ª ed., Wadsworth Publishing, 2005, ISBN 0-618-13384-4 .
- ( EN ) Michael Woods, Mary B. Woods, Ancient Machines: From Wedges to Waterwheels (Ancient Technology) , Runestone Press, 1999, ISBN 0-8225-2994-7 .
- ( EN ) Donald B. Wagner, Iron and Steel in Ancient China , EJ Brill, 1993, ISBN 90-04-09632-9 .
- ( EN ) Radomír Pleiner, Iron in Archaeology: The European Bloomery Smelters , Archeologický Ústav Av Cr., Praga, 2000, ISBN 978-80-86124-26-1 .
- ( EN ) Joseph Needham, Science and Civilization in China: Volume 4, Part 2 , Caves Books, Ltd., Taipei, 1986.
- ( EN ) Joseph Needham, Science and Civilization in China: Volume 4, Part 3 , Caves Books, Ltd., Taipei, 1986.
- Oleg D. Serby e Joffrey Wadsworth, Gli acciai di Damasco , in: Le scienze, nº 200, aprile 1985.
- Rosario Pinto, Il Paesaggio industriale , Print Art Edizioni, Nocera Superiore, 2016, 9788898887200
Voci correlate
- Siderurgia
- Ferro
- Acciaio
- Ghisa
- Metallurgia
- Centro siderurgico
- Altoforno
- Corex
- Fonderia
- Storia dell'industria italiana
- Ferriera alla genovese
- Tromba idroeolica
Altri progetti
-
Wikimedia Commons contiene immagini o altri file su storia della siderurgia
Collegamenti esterni
- Età del ferro ( PDF ), su scuoladecs.ti.ch .
- Ferro, acciai e ghise ( PDF ), su reolab.unimo.it .
- Produzione di acciaio , su infobuilddossier.it (archiviato dall' url originale il 28 novembre 2011) .
- L'età del ferro ( PDF ), su scuoladecs.ti.ch .
- Filmato didattico e interattivo sull'acciaio" ( SWF ), su promozioneacciaio.it .